Basic requirements for quality design of food processing machine products
The product quality design of food machine is to put forward quality requirements for products in the design of food machine, determine the product quality level (or quality grade), select the main performance parameters, specify economic and reasonable error ranges for various performance parameters, and establish tolerance standards and Other technical conditions, etc. Both the development of new products and the improvement of old products must go through the process of product quality design. The key to quality management of the food machine design process is to do a good job of product quality design. Conceptually, food machine product quality design is a user-driven and quality-driven integrated design idea. Its focus is on product quality, and it emphasizes the effective integration of quality into product design, rather than being outside the design.
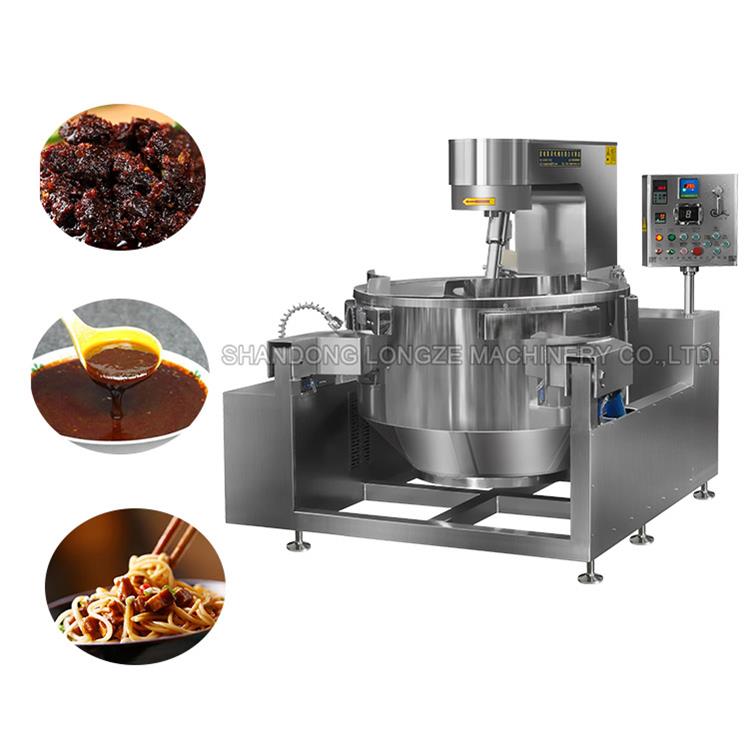
1. Product quality characteristics The quality characteristics of food machine products directly affect the applicability or degree of the product.
A more complex food machine can be composed of many parts, and each part contains many quality characteristics. If the value of each quality characteristic exceeds the prescribed limit, it will have different effects on product quality. Some quality characteristics, although not meeting the requirements of the design regulations, only slightly affect the function of the product; while others are not. If the requirements are not met, it may cause harm to personal safety and food safety, or to a lesser degree. Affect the product function adversely.
If these quality characteristics are mastered at design time, appropriate design methods, control methods and detection methods can be used to resolve the relevant risks. Therefore, in the production process of food machine, there must be important information about the quality requirements of safety, hygiene, function and so on. In addition, by grading the importance of the quality characteristics of food machine products and passing them to the process, manufacturing, inspection and procurement departments, these departments are making process plans, manufacturing quality control plans, process quality control plans, preparing test inspection plans and procurement In the control plan, focusing on preventive control measures can ensure the applicability of food machine product quality, which is a preventive control method or method for product quality.
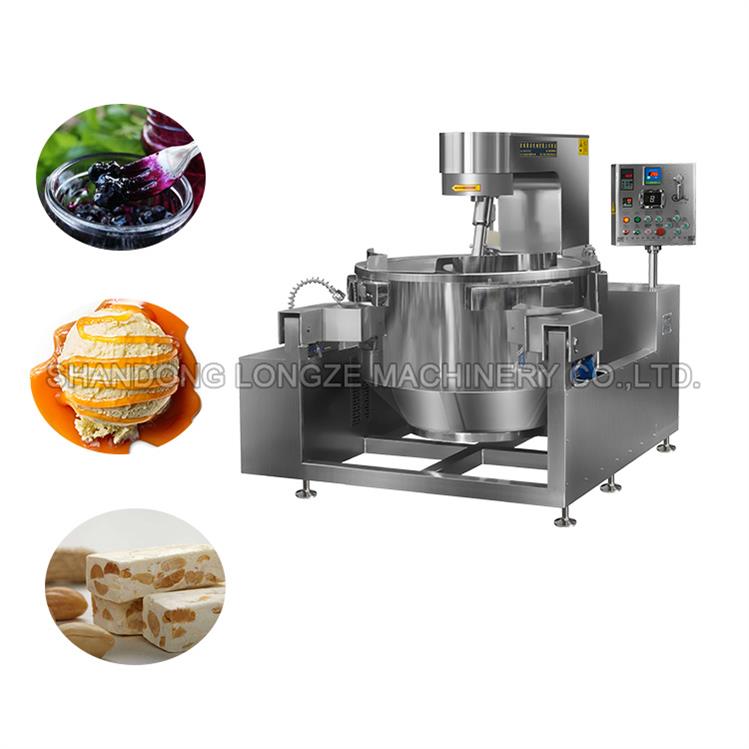
From the perspective of the development of the food machine manufacturing industry, its product quality has gone from product-oriented, manufacturing-oriented, and sales-oriented to today's market-oriented stage. In the product-oriented phase, product quality refers to the function expected by the product designer, that is, whether the evaluation standard of product quality is to achieve the expected functional requirements; in the manufacturing-oriented phase, product quality means compliance with product specifications, That is, in addition to achieving the expected functional requirements, the product quality evaluation standards must also meet the specified performance requirements; in the sales-oriented stage, product quality includes a series of measures for quality assurance in addition to making the product meet the specifications, such as To achieve "three guarantees" for products; in market-oriented today, product quality is defined as "a set of inherent characteristics of the product, the ability to meet the requirements of users and other beneficiaries", and its product quality characteristics refer to benefits from users and other The intrinsic characteristics of the product derived from the requirements of the product are an integral part of the product formation process.
Therefore, the quality of food machine products mentioned today refers to the ability to meet the needs of users and other beneficiaries in all aspects, including product function, technical performance, safety and health, reliability, adaptability, and economy. It can be seen that with the development of industrial technology and the improvement of productivity, the definition of product quality is constantly expanding.
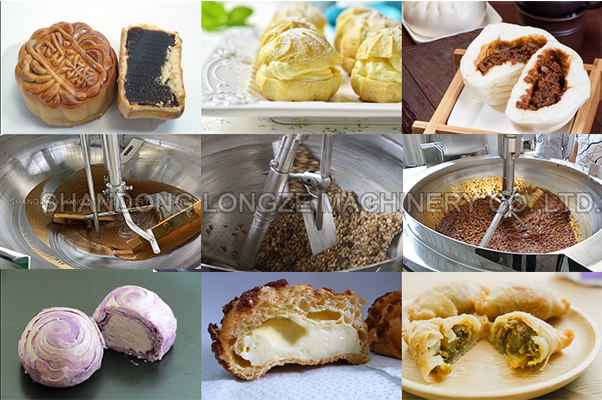
2. Tasks and steps of food processing machine product quality design
Basic tasks of food processing machine There are three basic tasks of food machine product quality design:
One is to ensure the functional quality of food machine. The designed food machine meets the technically specified functional goals to meet user needs.
The second is to ensure the quality cost of food machine. The production technology preparation cost, manufacturing cost and use cost of food machine are low, and the product has strong market competitiveness in price.
The third is to ensure the quality of food machine technical documents (including drawings). The technical documents must be able to correctly reflect the design ideas and technical requirements used to guide production. Avoid poor product quality and other losses due to poor design of drawings.
Statistics show that about 70% of the cost of food machine products is determined by design, and the proportion of cost of design work costs is much less than the proportion of manufacturing costs. If a scientific design method is adopted, the product cost can be greatly reduced.
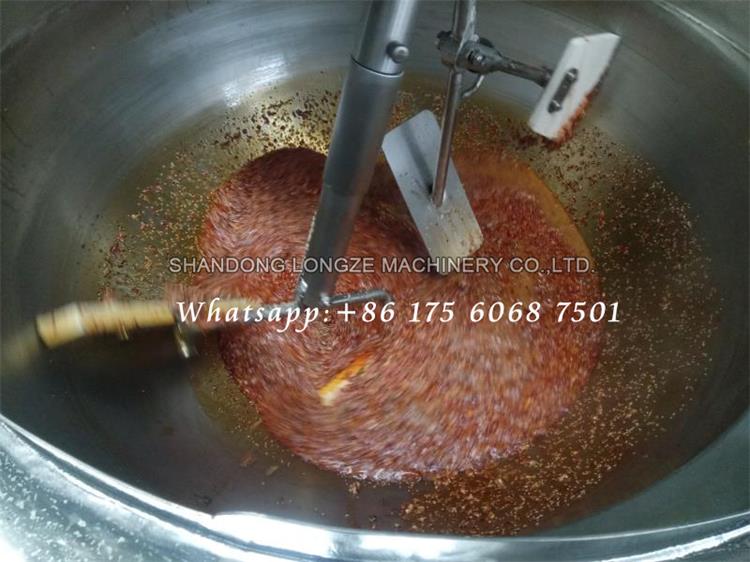
3. Contents of food processing machine product quality design
1 Collection and analysis of relevant information Technical information and quality information are the main basis for the development of new food machine products, and it has a great influence on the success or failure of the development of new products. Therefore, food processing machine manufacturing enterprises should establish technical information and quality information systems, and carry out comprehensive and unified management and use of various technical information and quality information.
2 The formulation of quality goals The quality goals of food machine products should be based on a thorough analysis of market dynamics, user requirements, and technical level, combined with the quality requirements and strength of food machine manufacturing enterprises, and adhere to the following principles: First, guarantee It has its own characteristics in similar products of the same grade. The second is to strive to become a high-end product of the same kind, with a high quality level. The third is that when high-end products cannot be realized, the cost of products in the same grade should be low.
3 Evaluation of product quality at different stages of food machine product development
There are different evaluation contents and emphasis:
The first is the planning, plan, and idea stage. The main purpose is to evaluate the product quality objectives. Its purpose is to communicate the opinions of the design, production, supply and marketing, quality and other departments in advance, and consider all important issues in the product development plan.
The second is the trial production and test stage of samples. Mainly evaluate the performance of food machine products, verify whether the product design is correct, and whether the product performance meets the program requirements.
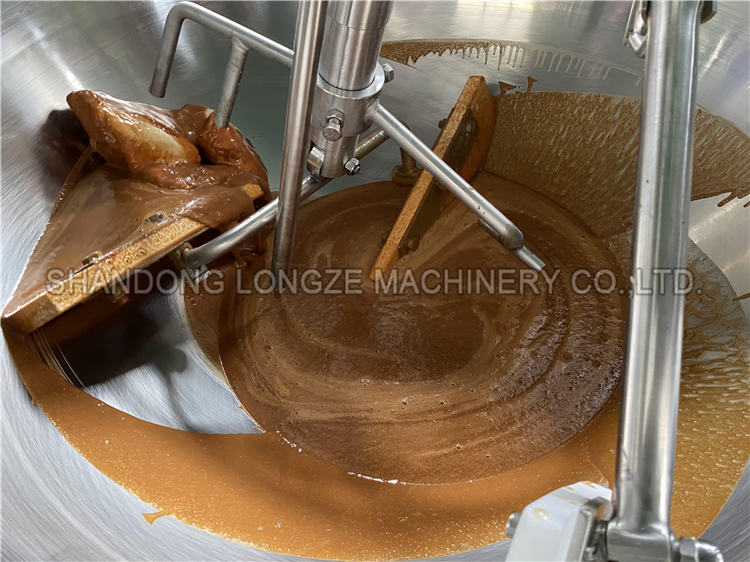
The third is the small batch trial production stage. Mainly evaluate the service life and effectiveness of the product, not only to comprehensively evaluate the various indicators of the product, but also to evaluate the preparations before commissioning to ensure the quality of the product after mass production.
The fourth is the mass production stage. Mainly evaluate the sales market, evaluate the use effect of products, collect user opinions and market demand, as a basis for further improvement of product quality.
4. The model of product quality design is based on relevant research results
We can divide the quality of food machine products into two categories:
One is external quality. Refers to the quality that users can feel, that is, the characteristics and characteristics of the final product.
The second is internal quality. Refers to the quality of production activities carried out within the enterprise to achieve external quality, including procurement, design, production, assembly and other qualities. Among them, the external quality reflects the relationship between the enterprise and the user, and is the user's quality requirements for the end product of the enterprise; while the internal quality reflects the relationship between the various departments within the enterprise, which is the product's internal flow in the enterprise. Quality requirements put forward by the next department. Each element in the external quality corresponds to the elements in the internal quality. The product quality design process is actually the process of ensuring the external quality by designing the corresponding internal quality.
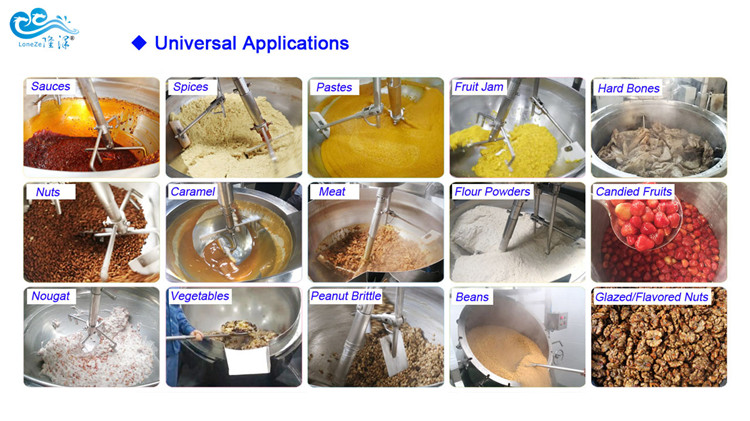
5. Method of product quality design
At present, there are many methods that can be used for the quality design of food machine products, which can be roughly divided into three categories according to their functions:
1 Design-oriented quality method The main function of this type of quality method is to assist people in food machine quality planning, quality design or quality improvement. For example, quality function configuration (QFD) is a powerful tool for user-driven product quality design; failure mode and its impact analysis (FMEA) can help people identify product quality problems as early as possible, avoid design errors, or take corresponding preventive measures during design To ensure product quality and improve design quality. Similarly, there are fault tree analysis (FTA), feature-factor graph analysis, failure mode and impact analysis (FMEA), failure mode and impact and lethality analysis (FMECA), event sequence tree analysis (ETA ), PHA, etc.
The product quality design of food machine is to put forward quality requirements for products in the design of food machine, determine the product quality level (or quality grade), select the main performance parameters, specify economic and reasonable error ranges for various performance parameters, and establish tolerance standards and Other technical conditions, etc. Both the development of new products and the improvement of old products must go through the process of product quality design. The key to quality management of the food machine design process is to do a good job of product quality design. Conceptually, food machine product quality design is a user-driven and quality-driven integrated design idea. Its focus is on product quality, and it emphasizes the effective integration of quality into product design, rather than being outside the design.
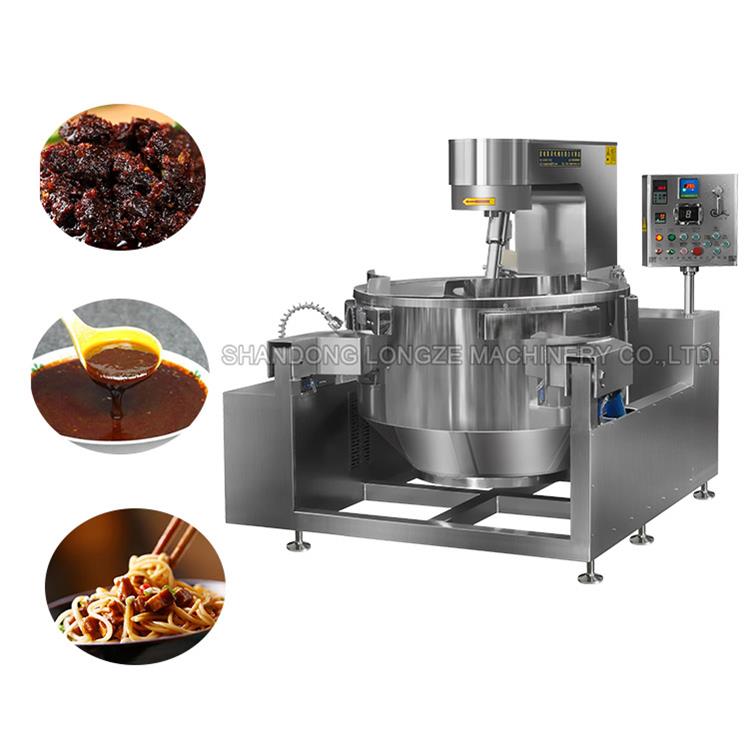
1. Product quality characteristics The quality characteristics of food machine products directly affect the applicability or degree of the product.
A more complex food machine can be composed of many parts, and each part contains many quality characteristics. If the value of each quality characteristic exceeds the prescribed limit, it will have different effects on product quality. Some quality characteristics, although not meeting the requirements of the design regulations, only slightly affect the function of the product; while others are not. If the requirements are not met, it may cause harm to personal safety and food safety, or to a lesser degree. Affect the product function adversely.
If these quality characteristics are mastered at design time, appropriate design methods, control methods and detection methods can be used to resolve the relevant risks. Therefore, in the production process of food machine, there must be important information about the quality requirements of safety, hygiene, function and so on. In addition, by grading the importance of the quality characteristics of food machine products and passing them to the process, manufacturing, inspection and procurement departments, these departments are making process plans, manufacturing quality control plans, process quality control plans, preparing test inspection plans and procurement In the control plan, focusing on preventive control measures can ensure the applicability of food machine product quality, which is a preventive control method or method for product quality.
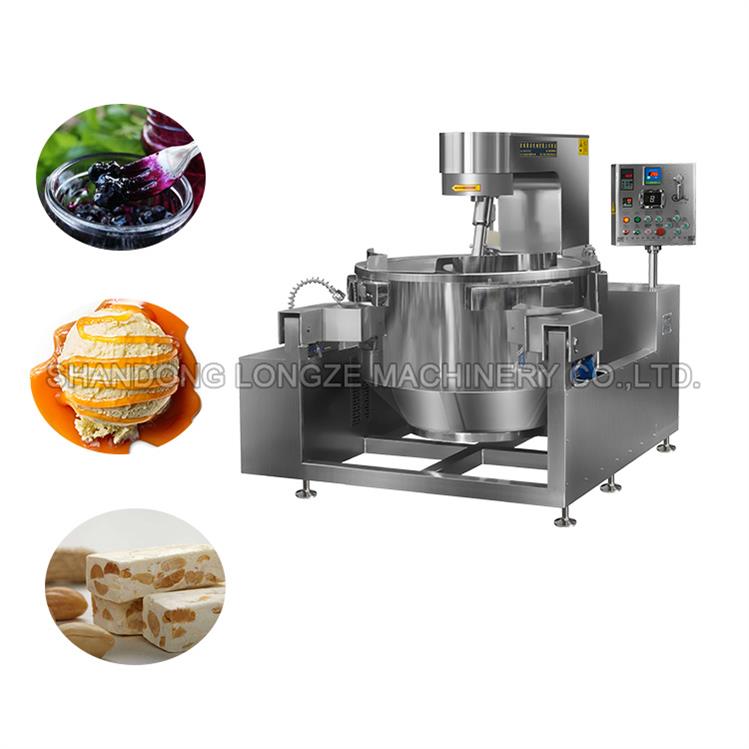
From the perspective of the development of the food machine manufacturing industry, its product quality has gone from product-oriented, manufacturing-oriented, and sales-oriented to today's market-oriented stage. In the product-oriented phase, product quality refers to the function expected by the product designer, that is, whether the evaluation standard of product quality is to achieve the expected functional requirements; in the manufacturing-oriented phase, product quality means compliance with product specifications, That is, in addition to achieving the expected functional requirements, the product quality evaluation standards must also meet the specified performance requirements; in the sales-oriented stage, product quality includes a series of measures for quality assurance in addition to making the product meet the specifications, such as To achieve "three guarantees" for products; in market-oriented today, product quality is defined as "a set of inherent characteristics of the product, the ability to meet the requirements of users and other beneficiaries", and its product quality characteristics refer to benefits from users and other The intrinsic characteristics of the product derived from the requirements of the product are an integral part of the product formation process.
Therefore, the quality of food machine products mentioned today refers to the ability to meet the needs of users and other beneficiaries in all aspects, including product function, technical performance, safety and health, reliability, adaptability, and economy. It can be seen that with the development of industrial technology and the improvement of productivity, the definition of product quality is constantly expanding.
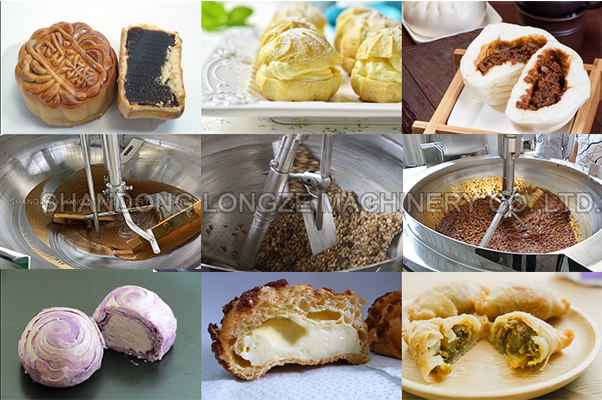
2. Tasks and steps of food processing machine product quality design
Basic tasks of food processing machine There are three basic tasks of food machine product quality design:
One is to ensure the functional quality of food machine. The designed food machine meets the technically specified functional goals to meet user needs.
The second is to ensure the quality cost of food machine. The production technology preparation cost, manufacturing cost and use cost of food machine are low, and the product has strong market competitiveness in price.
The third is to ensure the quality of food machine technical documents (including drawings). The technical documents must be able to correctly reflect the design ideas and technical requirements used to guide production. Avoid poor product quality and other losses due to poor design of drawings.
Statistics show that about 70% of the cost of food machine products is determined by design, and the proportion of cost of design work costs is much less than the proportion of manufacturing costs. If a scientific design method is adopted, the product cost can be greatly reduced.
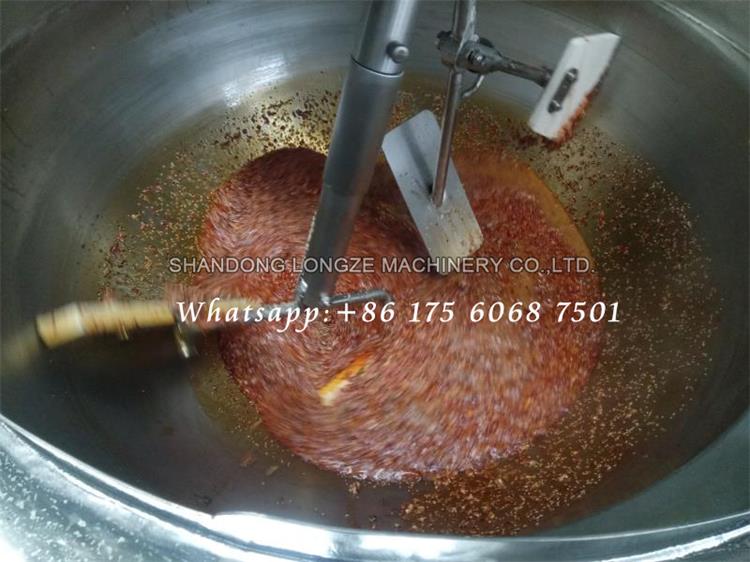
3. Contents of food processing machine product quality design
1 Collection and analysis of relevant information Technical information and quality information are the main basis for the development of new food machine products, and it has a great influence on the success or failure of the development of new products. Therefore, food processing machine manufacturing enterprises should establish technical information and quality information systems, and carry out comprehensive and unified management and use of various technical information and quality information.
2 The formulation of quality goals The quality goals of food machine products should be based on a thorough analysis of market dynamics, user requirements, and technical level, combined with the quality requirements and strength of food machine manufacturing enterprises, and adhere to the following principles: First, guarantee It has its own characteristics in similar products of the same grade. The second is to strive to become a high-end product of the same kind, with a high quality level. The third is that when high-end products cannot be realized, the cost of products in the same grade should be low.
3 Evaluation of product quality at different stages of food machine product development
There are different evaluation contents and emphasis:
The first is the planning, plan, and idea stage. The main purpose is to evaluate the product quality objectives. Its purpose is to communicate the opinions of the design, production, supply and marketing, quality and other departments in advance, and consider all important issues in the product development plan.
The second is the trial production and test stage of samples. Mainly evaluate the performance of food machine products, verify whether the product design is correct, and whether the product performance meets the program requirements.
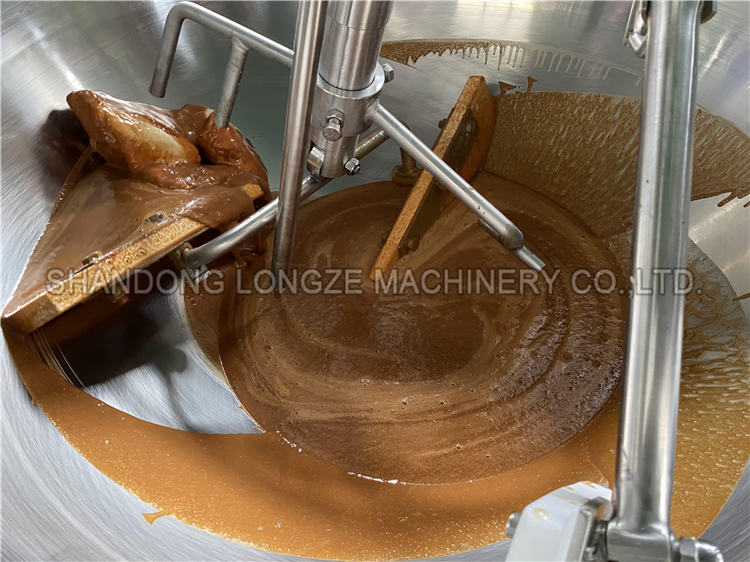
The third is the small batch trial production stage. Mainly evaluate the service life and effectiveness of the product, not only to comprehensively evaluate the various indicators of the product, but also to evaluate the preparations before commissioning to ensure the quality of the product after mass production.
The fourth is the mass production stage. Mainly evaluate the sales market, evaluate the use effect of products, collect user opinions and market demand, as a basis for further improvement of product quality.
4. The model of product quality design is based on relevant research results
We can divide the quality of food machine products into two categories:
One is external quality. Refers to the quality that users can feel, that is, the characteristics and characteristics of the final product.
The second is internal quality. Refers to the quality of production activities carried out within the enterprise to achieve external quality, including procurement, design, production, assembly and other qualities. Among them, the external quality reflects the relationship between the enterprise and the user, and is the user's quality requirements for the end product of the enterprise; while the internal quality reflects the relationship between the various departments within the enterprise, which is the product's internal flow in the enterprise. Quality requirements put forward by the next department. Each element in the external quality corresponds to the elements in the internal quality. The product quality design process is actually the process of ensuring the external quality by designing the corresponding internal quality.
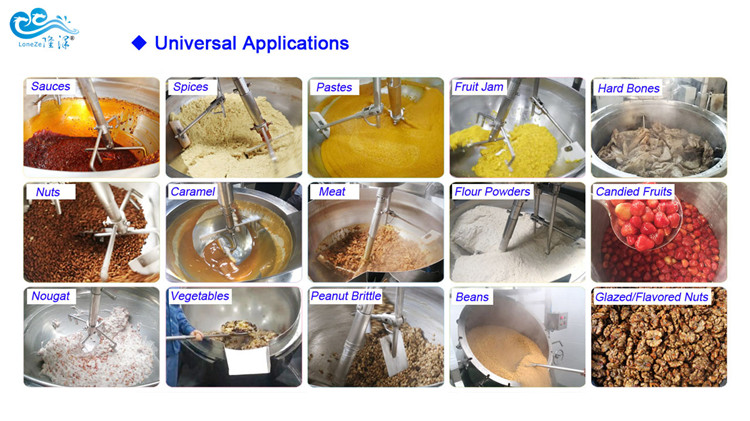
5. Method of product quality design
At present, there are many methods that can be used for the quality design of food machine products, which can be roughly divided into three categories according to their functions:
1 Design-oriented quality method The main function of this type of quality method is to assist people in food machine quality planning, quality design or quality improvement. For example, quality function configuration (QFD) is a powerful tool for user-driven product quality design; failure mode and its impact analysis (FMEA) can help people identify product quality problems as early as possible, avoid design errors, or take corresponding preventive measures during design To ensure product quality and improve design quality. Similarly, there are fault tree analysis (FTA), feature-factor graph analysis, failure mode and impact analysis (FMEA), failure mode and impact and lethality analysis (FMECA), event sequence tree analysis (ETA ), PHA, etc.
Please fill in the form and leave a clear message. We will contact you immediately.